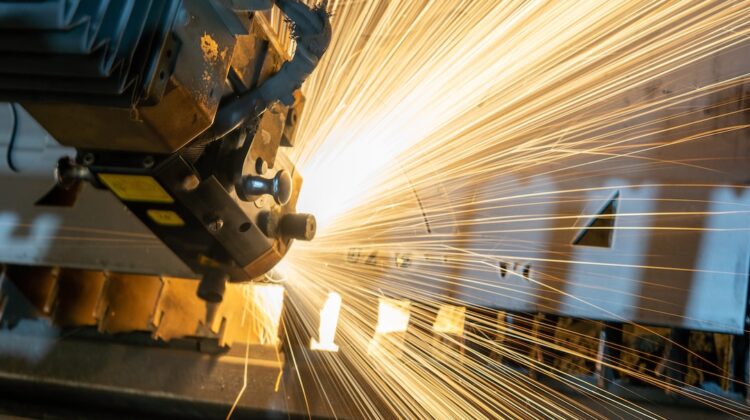
Reducing Energy Costs In The UK’s Manufacturing Of Electrical Equipment Industry
The UK’s electrical equipment manufacturing industry plays a crucial role in the country’s economy. It encompasses the production of a wide range of electrical equipment, including appliances, electronics, and components. This industry is known for its innovation and high-quality products, which are in demand both domestically and internationally.
In recent years, there has been a growing emphasis on energy efficiency in manufacturing. As energy costs continue to rise and environmental concerns become more pressing, businesses are recognizing the importance of reducing energy consumption and finding ways to operate more efficiently. This is particularly relevant for electrical equipment manufacturers, as their operations often require significant amounts of energy.
Summary
- The UK’s electrical equipment manufacturing industry is a significant contributor to the country’s economy.
- Reducing energy costs is crucial for manufacturers to remain competitive and sustainable.
- Energy efficiency measures such as upgrading equipment and implementing energy management systems can lead to significant cost savings.
- Technology such as smart sensors and automation can help manufacturers optimize energy usage and reduce waste.
- Renewable energy sources such as solar and wind power can provide a sustainable and cost-effective alternative to traditional energy sources.
The Importance of Reducing Energy Costs in Manufacturing
Energy costs can have a significant impact on manufacturing businesses. For electrical equipment manufacturers, energy consumption is a major expense that directly affects their bottom line. By reducing energy costs, businesses can improve their profitability and competitiveness in the market.
There are several benefits to reducing energy costs in manufacturing. Firstly, it helps to improve the overall efficiency of operations. By implementing energy-saving measures, businesses can optimize their processes and reduce waste. This not only saves money but also improves productivity and reduces downtime.
Secondly, reducing energy costs can help businesses meet their sustainability goals. As concerns about climate change and environmental impact grow, consumers and investors are increasingly looking for companies that prioritize sustainability. By implementing energy-saving measures, businesses can reduce their carbon footprint and demonstrate their commitment to environmental responsibility.
Energy Efficiency Measures for Electrical Equipment Manufacturers
There are several energy efficiency measures that electrical equipment manufacturers can implement to reduce their energy costs.
One of the most effective measures is investing in energy-efficient equipment and machinery. By replacing outdated or inefficient equipment with newer models that are designed to consume less energy, businesses can significantly reduce their energy consumption. This not only saves money but also improves the overall performance and reliability of the equipment.
Another important measure is upgrading lighting and HVAC systems. Lighting and heating, ventilation, and air conditioning (HVAC) are major energy consumers in manufacturing facilities. By upgrading to energy-efficient lighting systems and optimizing HVAC systems, businesses can reduce their energy consumption and improve the comfort and productivity of their employees.
Process optimization and automation are also key measures for improving energy efficiency in manufacturing. By analyzing and optimizing production processes, businesses can identify areas where energy is being wasted and implement changes to reduce consumption. Automation can also help to improve efficiency by reducing human error and optimizing energy usage.
The Role of Technology in Reducing Energy Costs
Technology plays a crucial role in reducing energy costs in manufacturing. There are several innovative technologies that businesses can leverage to improve energy efficiency.
Smart sensors and controls are one such technology. These devices can be installed throughout a manufacturing facility to monitor energy usage in real-time. By collecting data on energy consumption, businesses can identify areas where energy is being wasted and implement changes to reduce consumption. Smart controls can also be used to automate processes and optimize energy usage.
Predictive maintenance is another technology that can help to reduce energy costs. By using sensors and data analytics, businesses can predict when equipment is likely to fail and schedule maintenance before it becomes a problem. This not only reduces downtime but also improves the efficiency of equipment, leading to lower energy consumption.
Energy management software is also an important tool for reducing energy costs. This software allows businesses to track and analyze their energy usage, identify areas for improvement, and set targets for reducing consumption. It can also provide real-time alerts and notifications to help businesses stay on top of their energy usage.
Energy Auditing and Monitoring for Manufacturing Plants
Energy auditing is an important process for identifying areas where energy is being wasted and implementing changes to reduce consumption. It involves a comprehensive assessment of a manufacturing facility’s energy usage, including equipment, processes, and systems.
There are several types of energy audits that businesses can undertake. A basic energy audit involves a walkthrough of the facility to identify obvious areas for improvement, such as inefficient equipment or lighting. A more detailed energy audit involves a more in-depth analysis of energy usage, including data collection and analysis.
Continuous monitoring and tracking of energy usage is also important for identifying trends and patterns in energy consumption. By monitoring energy usage in real-time, businesses can identify areas where energy is being wasted and implement changes to reduce consumption. This can be done using smart sensors and controls, as mentioned earlier.
The Benefits of Renewable Energy Sources in Manufacturing
Renewable energy sources offer several benefits for electrical equipment manufacturers. These sources, such as solar and wind power, are clean and sustainable, making them an attractive option for businesses looking to reduce their carbon footprint.
One of the main benefits of using renewable energy in manufacturing is cost savings. While the upfront costs of installing renewable energy systems can be high, the long-term savings can be significant. Renewable energy systems generate electricity at a lower cost than traditional fossil fuel-based systems, resulting in lower energy bills for businesses.
Using renewable energy also helps businesses meet their sustainability goals. By reducing their reliance on fossil fuels and transitioning to clean energy sources, businesses can reduce their carbon footprint and contribute to a more sustainable future. This can also improve their reputation and attract environmentally conscious customers and investors.
There are several examples of renewable energy sources that can be used in manufacturing. Solar power is one of the most popular options, as it can be easily installed on rooftops or open spaces. Wind power is another option, particularly for businesses located in windy areas. Biomass and geothermal energy are also viable options for certain manufacturing facilities.
Government Incentives and Policies for Energy Efficiency
The UK government offers several incentives and policies to encourage businesses to prioritize energy efficiency.
One example is the Enhanced Capital Allowance (ECA) scheme, which allows businesses to claim 100% first-year capital allowances on investments in energy-saving equipment. This means that businesses can deduct the full cost of qualifying equipment from their taxable profits in the year of purchase, providing a significant financial incentive to invest in energy-saving technologies.
The government also offers grants and funding opportunities for businesses looking to implement energy-saving measures. For example, the Industrial Energy Transformation Fund provides funding for projects that reduce energy consumption and carbon emissions in manufacturing processes.
In addition to financial incentives, the government has also implemented policies and regulations to encourage businesses to improve their energy efficiency. For example, the Energy Savings Opportunity Scheme (ESOS) requires large businesses to undertake energy audits and identify cost-effective energy-saving measures.
Case Studies: Successful Energy Reduction Strategies in Electrical Equipment Manufacturing
There are several examples of successful energy reduction strategies in the electrical equipment manufacturing industry.
One example is a company that implemented a comprehensive energy management system, including smart sensors and controls, predictive maintenance, and energy management software. By monitoring and optimizing their energy usage, the company was able to reduce their energy costs by 20% and improve their overall efficiency.
Another example is a company that invested in renewable energy sources, such as solar power. By installing solar panels on their facility, the company was able to generate a significant portion of their electricity needs on-site, resulting in substantial cost savings.
Challenges and Barriers to Energy Efficiency in Manufacturing
While there are many benefits to improving energy efficiency in manufacturing, there are also several challenges and barriers that businesses may face.
One common challenge is the upfront cost of implementing energy-saving measures. While these measures can result in long-term cost savings, the initial investment can be significant. This can be a barrier for small and medium-sized businesses that may not have the financial resources to invest in energy-saving technologies.
Another challenge is the lack of awareness and understanding of energy-saving technologies and practices. Many businesses may not be aware of the potential cost savings and environmental benefits of improving energy efficiency. This can make it difficult to convince businesses to invest in energy-saving measures.
There may also be technical challenges associated with implementing energy-saving measures. For example, retrofitting existing equipment or systems to make them more energy-efficient can be complex and require specialized knowledge and expertise.
The Future of Energy Efficiency in the UK’s Electrical Equipment Manufacturing Industry
The future of energy efficiency in the UK’s electrical equipment manufacturing industry looks promising. As energy costs continue to rise and environmental concerns become more pressing, businesses are likely to prioritize energy efficiency and invest in energy-saving technologies.
There are several trends and predictions for energy efficiency in manufacturing. One trend is the increasing use of automation and artificial intelligence to optimize energy usage. By using advanced analytics and machine learning algorithms, businesses can identify patterns and trends in energy consumption and implement changes to reduce waste.
Another trend is the integration of renewable energy sources into manufacturing processes. As renewable energy technologies become more affordable and efficient, businesses are likely to transition away from fossil fuels and rely more on clean energy sources.
Opportunities for growth and innovation in the energy efficiency sector are also expected. As businesses become more aware of the benefits of improving energy efficiency, there will be a growing demand for innovative solutions and technologies that can help them achieve their goals.
In conclusion, energy efficiency is a crucial consideration for electrical equipment manufacturers in the UK. By reducing energy costs, businesses can improve their profitability, meet sustainability goals, and gain a competitive edge in the market. There are several measures that businesses can implement to improve energy efficiency, including investing in energy-efficient equipment, upgrading lighting and HVAC systems, optimizing processes, and leveraging technology. Government incentives and policies also provide financial support and regulatory frameworks to encourage businesses to prioritize energy efficiency. By prioritizing energy efficiency, businesses can not only save money but also contribute to a more sustainable future.
If you’re interested in learning more about reducing energy costs in the UK’s manufacturing of electrical equipment industry, you should definitely check out this informative article on Cut My Utility Bills’ blog. The article titled “Hello World!” provides valuable insights and practical tips on how manufacturers can effectively lower their energy expenses while maintaining productivity and sustainability. It’s a must-read for anyone in the industry looking to optimize their operations and contribute to a greener future. Read more
FAQs
What is the electrical equipment manufacturing industry in the UK?
The electrical equipment manufacturing industry in the UK involves the production of various electrical equipment such as transformers, generators, switchgear, and other related products.
What are the energy costs associated with the electrical equipment manufacturing industry in the UK?
The energy costs associated with the electrical equipment manufacturing industry in the UK are significant due to the high energy consumption required for the production process.
Why is reducing energy costs important for the electrical equipment manufacturing industry in the UK?
Reducing energy costs is important for the electrical equipment manufacturing industry in the UK as it can help to improve the industry’s competitiveness, reduce carbon emissions, and increase profitability.
What are some ways to reduce energy costs in the electrical equipment manufacturing industry in the UK?
Some ways to reduce energy costs in the electrical equipment manufacturing industry in the UK include investing in energy-efficient equipment, implementing energy management systems, and optimizing production processes.
What are the benefits of reducing energy costs in the electrical equipment manufacturing industry in the UK?
The benefits of reducing energy costs in the electrical equipment manufacturing industry in the UK include improved competitiveness, reduced carbon emissions, increased profitability, and improved sustainability.